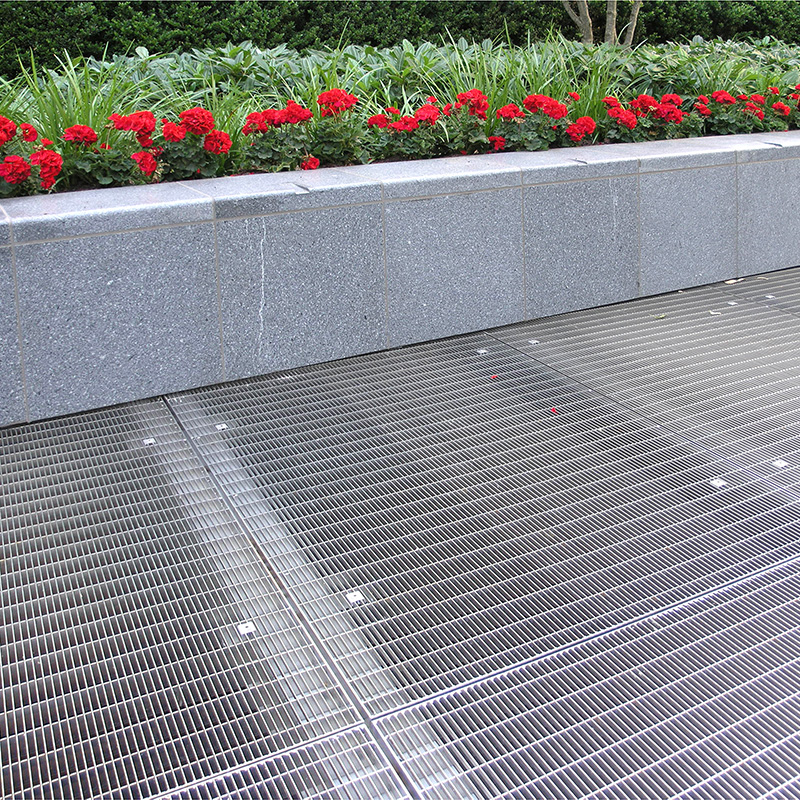
The Importance of High-Quality Welding for Aluminum Grating
Table of Contents
Welding Challenges with Aluminum Grating
High-quality welding is essential for ensuring the structural integrity and optimal performance of aluminum grating. Due to its lightweight, corrosion-resistant, and high-strength properties, aluminum grating is widely utilized across various industries. However, welding aluminum presents unique challenges that require specialized techniques and meticulous attention to detail.
Choosing the Right Welding Process For Aluminum Bar Gratings
One of the critical considerations in welding aluminum is selecting the appropriate welding process. Techniques such as TIG (Tungsten Inert Gas) or MIG (Metal Inert Gas) welding are commonly used because they produce clean and precise welds. Other methods, including laser beam, electron beam, resistance welding, and shielded metal arc welding, can also be employed based on the specific project requirements.
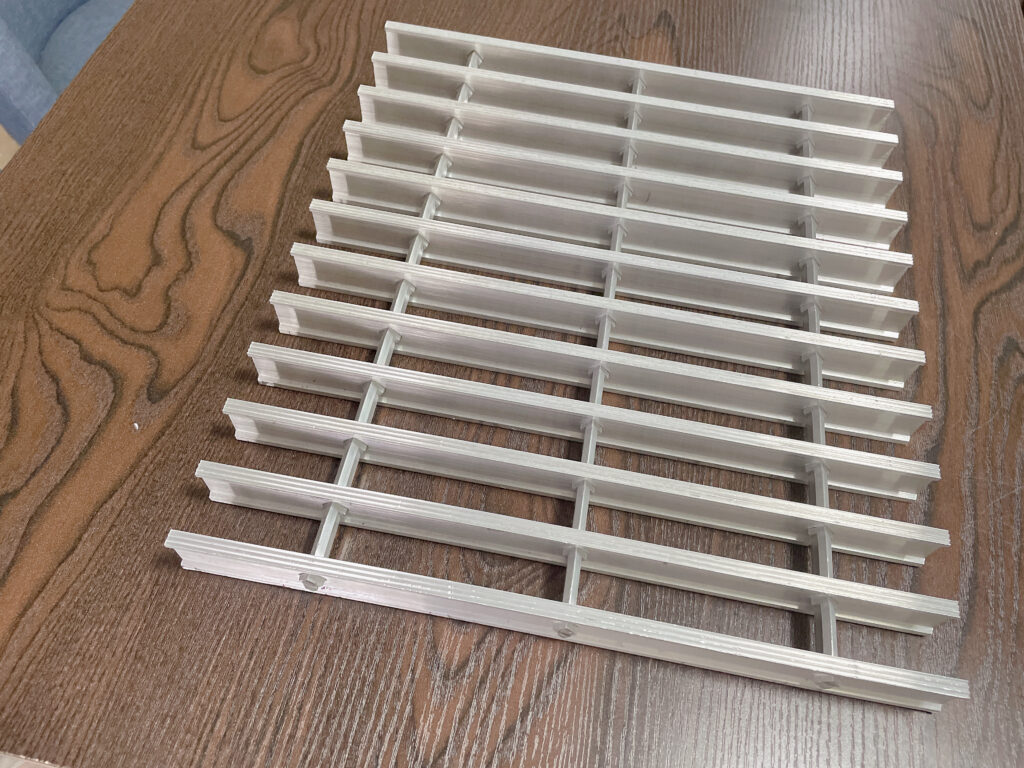
Aluminum's High Thermal Conductivity
Aluminum’s high thermal conductivity and its tendency to form an oxide layer complicate the welding process. The material dissipates heat rapidly, which can lead to insufficient fusion and weak welds if not managed correctly. Additionally, the formation of oxides necessitates thorough cleaning and preparation of the material before welding to ensure strong and defect-free joints.
Importance of Appropriate Filler Metals
Using the appropriate filler metals is crucial for achieving high-quality welds. For instance, welding a 6061 aluminum alloy base material often requires the use of 5356 or 4043 aluminum filler metals to avoid common welding issues such as cracking and porosity. Specific wire feeding systems may also be necessary to handle aluminum’s lower column strength compared to steel, preventing buckling and tangling during the welding process.
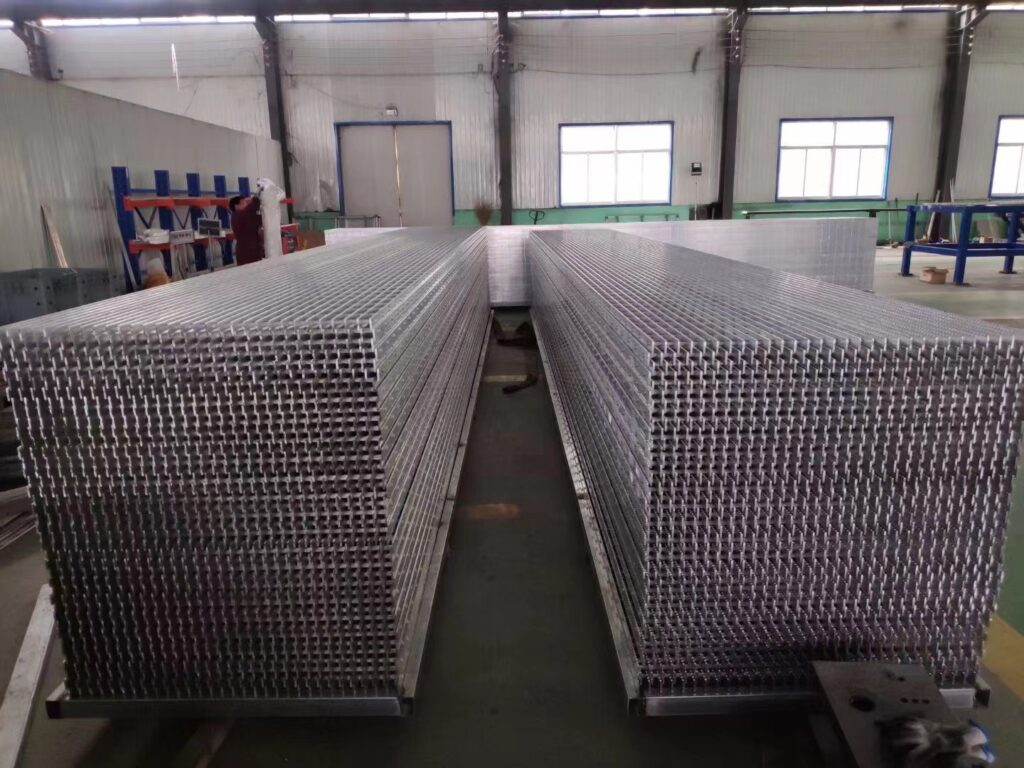
Load-Carrying Capacity and Durability Of Aluminum Bar Gratings
The significance of proper welding extends beyond the immediate mechanical properties. High-quality welds ensure that aluminum grating maintains its load-carrying capacity and durability over time. This is particularly important in applications that demand stringent load requirements, such as pedestrian or vehicular loads.
Enhancing Longevity and Safety of Aluminum Bar Gratings
In industrial settings, well-executed welds enhance the longevity and safety of aluminum grating by improving its structural integrity and resistance to wear and tear. Moreover, high-quality welding practices are vital for maintaining aluminum grating’s inherent properties, such as corrosion resistance. Regular inspections and the application of protective coatings can mitigate corrosion, especially in harsh environments. This helps preserve the grating’s performance and extend its lifespan, which is crucial for applications in corrosive environments like chemical industries and marine superstructures.
Conclusion
In conclusion, the excellence of aluminum grating welding is pivotal for its performance and durability.
Our extensive experience and commitment to high-quality welding practices set us apart in the industry. With a rich history of delivering superior aluminum grating solutions, we excel in overcoming the unique challenges of welding aluminum. This expertise ensures that our gratings offer exceptional structural integrity, load-carrying capacity, and longevity, making them a reliable choice for diverse applications.
Comments
Tags
Frequently Asked Question
Welding aluminum grating presents unique challenges due to aluminum’s high thermal conductivity and the tendency to form an oxide layer. These factors require specialized techniques and meticulous preparation to ensure strong and defect-free welds.
TIG (Tungsten Inert Gas) and MIG (Metal Inert Gas) welding are commonly used for aluminum grating due to their ability to produce clean and precise welds. Other methods, such as laser beam and electron beam welding, can also be used depending on project requirements.
The choice of filler metals, such as 5356 or 4043 for 6061 aluminum alloy, is crucial to prevent common issues like cracking and porosity. Using appropriate filler metals ensures high-quality welds and the structural integrity of the grating.
High-quality welding ensures that aluminum grating maintains its load-carrying capacity and durability over time. It enhances the grating’s structural integrity, resistance to wear and tear, and overall longevity, making it suitable for demanding applications.