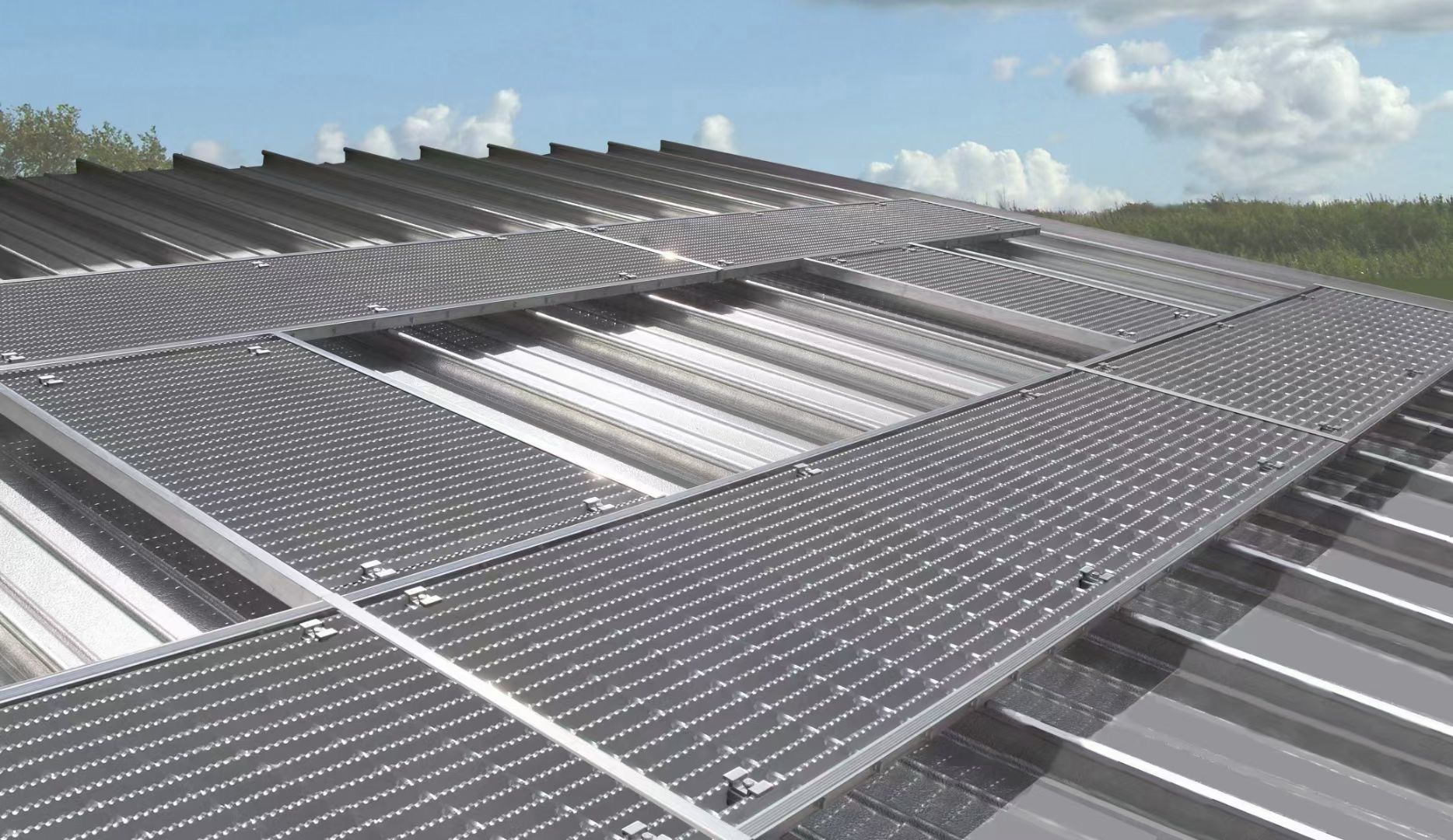
A Deep Look For Metal Grating
Table of Contents
Definition and Applications of Metal Grating
Metal grating is a product formed by creating a grid from perforated metal sheets or by assembling metal bars. It is extensively utilized across various industries for applications such as stairs, platforms, scaffolding, and protective coverings. The production methods for metal gratings include expansion, perforation, molding, and welding.
Historical Development of Metal Grating
Initially, metal grating was developed to ventilate underground spaces that would otherwise become overheated and unsanitary. During World War II, it evolved into a versatile and quick-to-assemble solution for installing runways and emergency surfaces, often referred to as magic carpets.
Production Parameters for Metal Grating
The production of metal gratings is based on several parameters, including the thickness of the material, the dimensions of the metal bars, the pattern of the openings, load capacity, and the specific location or environment of installation. Metal grating’s flexibility allows for the purchase of standard sizes or the customization of designs to meet specific application needs. Custom designs are frequently required, as installations often have unique specifications.
Terminology for Metal Grating
Various metals can be used to produce metal gratings, with common types being iron, carbon steel, aluminum, and stainless steel. These gratings are typically employed as non-slip surfaces in applications requiring a secure work platform.
Metal gratings come in an extensive range of patterns, designs, and configurations, including combinations of steel grating and steel plates. They can be manufactured to be welded, press-locked, dense, or compounded with metal plates, making them suitable for demanding and rigorous conditions.
Design and Choose of Metal Gratings
When designing metal grating, factors such as the required passage of light, air, and sound are considered, along with the aesthetic value based on the grating’s visibility. Heavier gratings are typically constructed from welded steel or pressure-locked interlocked bars.
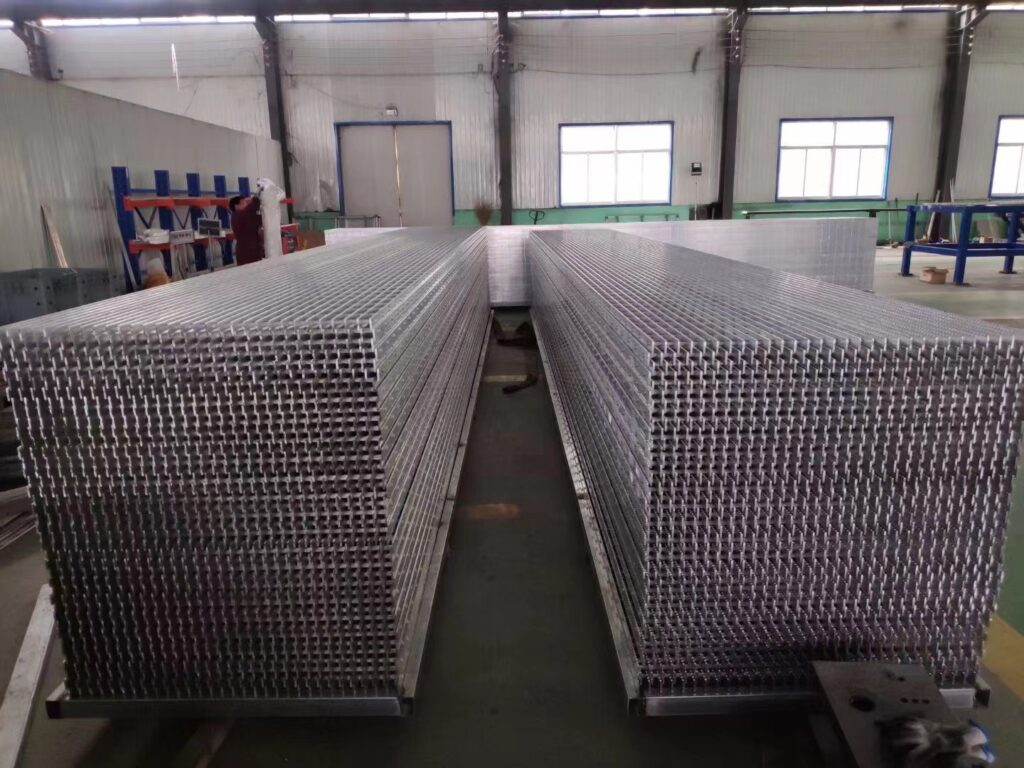
Overview of Metal Grating Types Varieties
Engineers and designers develop metal grating solutions tailored to the structural specifications. Their considerations include the thickness, dimensions of the metal bars, and the pattern of the openings, which can be oval, square, or diamond-shaped.
When designing metal grating, factors such as the required passage of light, air, and sound are considered, along with the aesthetic value based on the grating’s visibility. Heavier gratings are typically constructed from welded steel or pressure-locked interlocked bars.
Expanded Metal Gratings
Expanded metal grating is named for its manufacturing process, where metal sheets are punctured with slits and then stretched, creating a diamond-shaped pattern. These sheets can be cut to fit various applications and can be made from different types of metals.
Standard expanded metal grating is slip-resistant, while flattened expanded metal grating is cold-rolled for a smooth finish. Non-flattened expanded metal grating has a raised surface for better traction.
Bar Metal Grating
Bar metal grating, the most common type, consists of parallel bars connected to perpendicular bars through methods such as welding, riveting, close meshing, and press locking. Made from aluminum or steel, bar grating offers a high strength-to-weight ratio, making it ideal for industrial flooring, fire escapes, street drains, and bridges due to its durability and strength.
Wire Mesh Metal Grating
Also known as wire fabric or wire cloth, wire mesh metal grating features intersecting rows and columns of wires. It’s easy to install, highly durable, and used in various industries. This grating can be welded or woven, with welded wire grating having intersecting points welded and woven wire grating having rows and columns woven over and under each other.
Perforated Metal Grating
Perforated metal grating is created by stamping, punching, or deforming metal sheets to form holes of specific sizes, patterns, and shapes. Made from robust metals like stainless steel, carbon steel, and aluminum, perforated grating is used for sound reduction, ventilation, and screening.
Safety or Grip Strut Grating
Designed for traction and safety, grip strut grating provides a firm, skid-resistant surface with diamond protrusions for enhanced grip. It features large openings for drainage and airflow, with serrated diamond edges to increase traction, produced through cold stamping.
Compound Metal Grating
Combining bar grating and steel plate grating, compound metal grating consists of a checkered plate sealed to a steel bar grating surface. It comes in various sizes and materials, including combinations with wire mesh or multiple layers of bar and perforated metal grating. Heavy gauge steel is used to prevent deformation during zinc coating.
Press Locked Metal Grating
Press locked metal grating is a type of bar grating where cross and bearing bars are notched and pressed together, creating a smooth, even surface. This aesthetically pleasing grating is used in architectural designs and is available in steel and aluminum, with a range of sizes and bar openings.
Varieties of Metals Utilized in Metal Gratings
The term “grating” encompasses any framework or covering used for protecting openings, providing support, serving as platforms, or offering safety. Various materials are employed to produce grating, ranging from durable plastics to robust steel and stainless steel. When selecting a grating material, key considerations include the application environment, required strength, and aesthetic contribution to the structure.
Metal gratings serve diverse conditions and environments as safety measures or protective solutions. They are commonly used in airports, industrial settings, and manufacturing facilities due to their strength and durability.
Aluminum Metal Grating
Aluminum gratings are known for their malleability, corrosion resistance, ductility, and thermal and electrical conductivity. They are lightweight, non-toxic, non-magnetic, and resistant to bacterial growth. Aluminum gratings can endure extreme cold without becoming brittle. Their widespread use is attributed to their attractive appearance, making them suitable for both industrial and decorative purposes.
Light-Duty Steel Grating
Light-duty steel gratings cater to pedestrian traffic and some rolling traffic, like carts and hand trucks. Produced as bar grating, they can be swaged, riveted, dovetailed, or welded. Typically, light-duty steel gratings feature load-bearing bars with perpendicular cross bars and are made from carbon steel with an open grid structure. Due to their cost efficiency and low maintenance, they are commonly used for highway platforms, safety barriers, and machinery floors.
Stainless Steel Gratings
Multiple grades of stainless steel, such as 304, 304L, 316, and 316L, are used to produce metal grating. Stainless steel gratings are exceptionally strong, durable, and capable of withstanding corrosive, humid, and high-moisture conditions. They are made using various bar sizes through swaging or welding methods. Stainless steel’s unique properties make it ideal for water treatment plants, chemical processing facilities, and oil and gas production, due to its resilience and ability to endure harsh weather and temperature fluctuations.
Galvanized Steel Grating
Galvanized steel, carbon steel coated with zinc, offers protection against rust and corrosion. Like stainless steel, galvanized steel is perfect for outdoor installations or environments with high moisture. The zinc coating ages slowly, extending the lifespan of the grating. Most galvanized steel gratings fall under the B load class, capable of supporting 28,000 lbs or 125 kilonewtons (kN), as classified by the Deutsches Institut für Normung (DIN).
Heavy-Duty Carbon Steel Grating
Heavy-duty carbon steel gratings use thicker and deeper steel bars, joined at high temperatures to form a secure and solid joint. These gratings are designed to bear heavy loads and provide optimal performance for extended periods.
Manufacturing Methods of Metal Grating
Different types of metal gratings are manufactured using various methods, depending on the materials and production techniques. Common methods include welding, dovetailing, stretching, and swaging, with welding being the most frequently used. The selection of the method is based on the material’s thickness, weight, and intended use.
Regardless of the method, the initial step is choosing the metal, determined by the environmental conditions and the required strength and durability of the grating.
Expanded Metal Grating Process
The production of expanded metal grating starts with metal sheets that are slit into a diamond pattern. This process is completed in a single operation where diamond-shaped slits are cut into the metal sheets as they are stretched.
Piercing and stretching create a raised surface with bonds and strands at a uniform angle to the metal sheet plane, resulting in a grating with excellent strength and rigidity. For applications requiring a smooth surface, the expanded metal sheets are flattened between rollers.
Non-flattened expanded metal grating, known as raised metal grating, has a three-dimensional appearance, enhancing its strength and rigidity. It is widely used for platforms, walkways, protective panels, speaker grills, and fluid or air filters. The key feature of non-flattened metal grating is its ability to add structural strength and stability.
Swaging Process
Swaging is a cold metalworking process where metal is deformed to fit into another part by force. In metal grating production, the process starts with load-bearing metal bars spaced evenly for strength and design. Tubular bars are then placed across these load-bearing bars and welded. The bars’ depth and spacing vary based on the grating’s intended use.
Dovetail (DT) Manufacturing
Dovetailing, an ancient method used for centuries, joins two materials by precision slotting the load-bearing and cross bars, ensuring a tight fit. Once positioned, a hydraulic press forces the metal pieces together, creating a permanent lock with a rigid flat surface. This interlocking design provides stability and load distribution, making DT-manufactured metal gratings suitable for areas needing drainage and accommodating high-heeled traffic.
Welded Metal Grating Production
Welded metal grating is made using an electro-forging process where rectangular load-bearing bars are welded to cross bars, creating a durable and long-lasting connection. These gratings, with bearing bars ranging from 0.125 to 0.5 inches thick, are used in various applications and can be left bare, painted, or hot-dip galvanized. Specialty finishes include enamel, epoxy paints, or powder coatings.
Riveted Metal Grating
Produced using carbon steel, 6000 series aluminum, and 300 series stainless steel, riveted metal grating involves riveting crimped flat bars to load-bearing bars in a reticulated pattern. This method results in gratings with high resistance to impact, fatigue, and heavy loads, providing excellent strength and durability under stress.
Banding in Metal Gratings
Metal gratings are often open-ended but can be reinforced with banding—flat metal bars welded to the grating panel ends. Banding increases stiffness and provides a finished look, essential for removable gratings to ensure safety during replacement and removal. For motor traffic, banding reduces impact loads on adjacent bars and resists deformation. Trench banding, with the band bar above the load-bearing bars, is used in drainage applications for efficient drainage.
Mechanical Fasteners
Various mechanical fasteners friction-connect metal gratings, available in different sizes and types to suit various grating forms.
- Saddle Clips: Bent clips bridging bearing bars, commonly used as grating anchors and secured to the base structure with fasteners, though not for heavy-duty applications.
- “G” Clips: Three-part clips with a top clip for holding the bearing bar, a tapped bottom clip, and a hex bolt to connect them. The top clip is tightened by connecting to the bottom clip.
- Weld Lugs: Welded between bearing bars to bolt the grating to the supporting structure.
- Countersunk Land: Used for narrow-spaced gratings, allowing countersunk bolt shoulders for flat head screws or self-drilling screws to secure the grating.
- “J” Clips: Shaped like a “J”, with the long part extending over the bearing bar and the bottom resting on the supporting structure, fastened in place, often used where space is limited.
Standards for Metal Grating
Like all industrial products, metal gratings adhere to specific standards set to ensure quality and performance. Two primary sets of standards commonly referenced are those by the American National Standards Institute (ANSI) and the Deutsches Institut für Normung (DIN), also known as the German Institute for Standardization.
American National Standards Institute (ANSI)
ANSI categorizes metal grating standards into five groups based on weight capacity:
- Light Duty: Supports loads under 2000 lbs (900 kg), suitable for pedestrian use only.
- Medium Duty: Handles loads between 2000 lbs and 5000 lbs (900 kg and 2250 kg), ideal for light pneumatic traffic, sidewalks, and residential parking areas.
- Heavy Duty: Can support loads from 5000 lbs to 7500 lbs (2250 kg to 3375 kg), suitable for commercial traffic and tractor trailers.
- Extra Heavy Duty: Designed for roads, highways, and bridges, with an H-20 load rating, capable of handling up to 10,000 lbs (4500 kg).
- Special Duty: Built to withstand airport traffic, handling loads of 10,000 lbs (4500 kg) or more.
German Institute for Standardization (DIN)
DIN classifications range from A to F, each designated for specific load capacities and applications:
- Load Class A: For pedestrian traffic, supporting up to 3370 lbs (15 kilonewtons, kn).
- Load Class B: Suitable for parking lots, sidewalks, and light vehicles, with a load rating of 28,000 lbs (125 kn).
- Load Class C: Handles commercial applications, supporting up to 56,000 lbs (250 kn).
- Load Class D: Designed for very heavy loads, with an H-20 load rating, capable of 90,000 lbs (400 kn). Suitable for forklifts, roads, bridges, and highways.
- Load Class E: Handles diverse manufacturing and transportation conditions, including high-impact steel struts and metal wheels, with a rating of 134,000 lbs (600 kn).
- Load Class F: Built for airport traffic, supporting over 200,000 lbs (900 kn).
These standards guide manufacturers in producing metal gratings that meet specific load and environmental requirements, ensuring safety and reliability across various applications.
4 Applications of Metal Grating
Metal grating finds extensive use as a safety measure, providing a reliable and firm work surface with excellent grip. It also functions as a protective barrier to avert accidents in risky situations.
The use of metal gratings is determined by the material they are made from. Aluminum and stainless steel are perfect for corrosive and damp environments, while carbon steel is favored for heavy-duty tasks due to its robustness.
Metal Gratings in Construction
Metal gratings are frequently employed in construction for flooring, walkways, platforms, and mezzanines due to their visual appeal and longevity. Their sturdy and secure structure makes them ideal for enhancing any building, providing a unified and protective layer.
Gratings in Filtration Systems
Metal gratings play a vital role in water filtration systems thanks to their resistance to corrosion and high strength. They are used to capture large debris such as plastic bags and boxes, offering efficient filtration with low material usage and a long service life.
Metal Grating for Flooring
Metal grating is commonly utilized as flooring. Aluminum floor grates are ideal for marine and wastewater settings due to their lightweight nature, allowing for easy handling in tight spaces. Steel floor grating is used in heavy-duty applications, offering a durable and rough surface suitable for industrial facilities.
Fencing with Metal Grating
Metal grating fences provide a visually appealing appearance along with the necessary strength and rigidity for high security. The firm connection between panels makes them perfect for areas requiring protection from intruders. Metal grating fences can be tailored to fit any location’s dimensions, offering both security and aesthetic appeal.
What Can We Offer You?
As an aluminum bar gratings factory with 15 years of manufacturing history, we can produce standard and customized aluminum swaged bar gratings, press locked gratings, and stainless steel gratings. We focus on high-standard and high-quality grating needs.
Our advantages include:
1. Aluminum bar gratings source factory, capacity per day is more than 400M2.
2. We have an experienced technical team and have participated in international project construction needs.
3. Our welders have international advanced welding technology, welders and welding process are verified by SGS.
4. We have the experience to undertake customized aluminum bar grating projects of more than 30,000 square meters.
If you have metal gratings requirements or related questions, please contact us. Our professional team will contact you within 2 hours.
Comments
Tags
Frequently Asked Question
Metal gratings are typically made from aluminum, stainless steel, and carbon steel. Aluminum and stainless steel are ideal for corrosive and moist environments due to their resistance to rust and corrosion. Carbon steel is preferred for heavy-duty applications because of its strength and durability.
In construction, metal grating is commonly used for flooring, walkways, platforms, and mezzanines. Its strong, durable, and safe structure makes it ideal for providing a stable surface and adding an extra dimension to buildings, ensuring both safety and aesthetic appeal.
Metal gratings are essential in water filtration systems because they can resist corrosion and provide exceptional strength. They are used to filter out large debris such as plastic bags and boxes, ensuring efficient filtration with minimal material consumption and a long service life.
Metal grating fences offer a combination of strength, rigidity, and visual appeal. They provide high security due to their secure connections between panels, making them suitable for areas needing protection from intruders. Additionally, metal grating fences can be customized to fit any location’s dimensions, providing both security and aesthetic value.