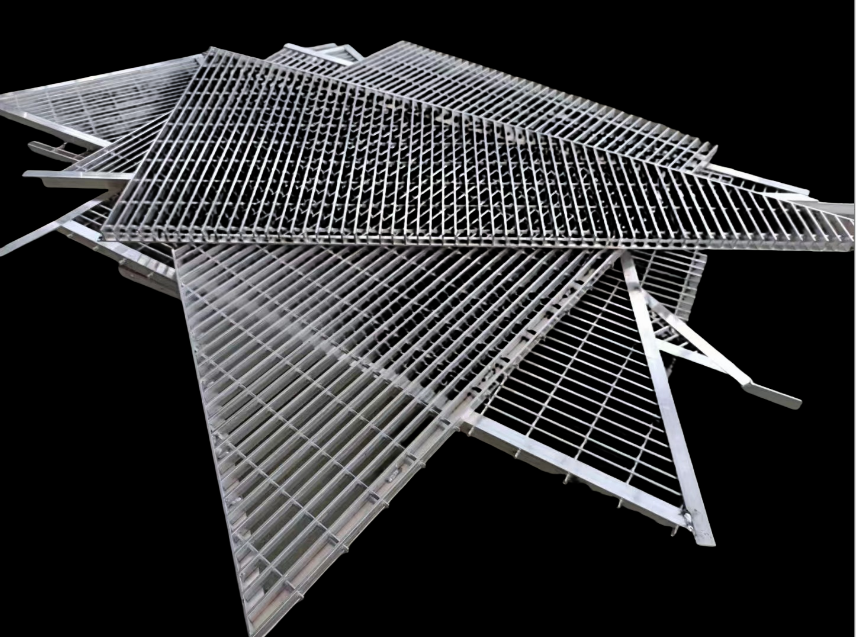
How to install aluminum bar grating in New York?
Table of Contents
Installation of Aluminum Bar Gratings
When installing aluminum bar grating in New York, it is essential to adhere to best practices to ensure safety, durability, and regulatory compliance. Proper installation not only extends the lifespan of the aluminum bar grating but also ensures optimal performance in various applications, from industrial to commercial settings. Today we will share the key guidelines and considerations to install aluminum bar gratings.
Correct Orientation of Aluminum Bar Grating
One of the fundamental installation requirements is to position the grating with the cross rods on the top side. This configuration is crucial as it aligns with the manufacturer’s strength specifications, ensuring the aluminum bar grating can withstand the designed load capacity. Misalignment could compromise structural integrity and safety.
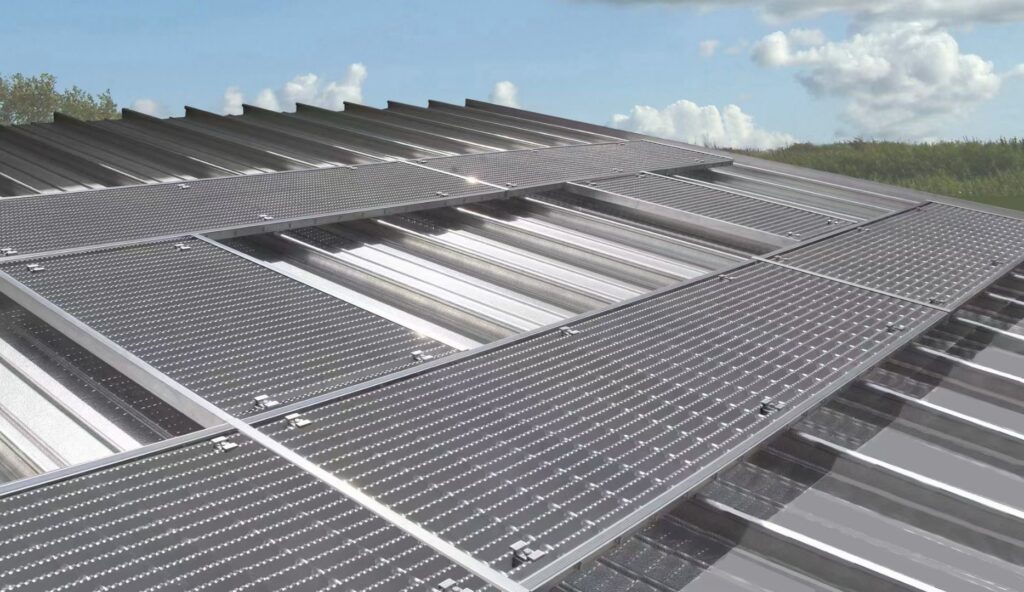
Material Requirements for Supports
To maintain the overall structural integrity of the installation, it is mandatory that all aluminum bar grating supports are constructed from metal. Metal supports provide the necessary strength and stability, particularly in high-load environments, preventing any potential sagging or failure over time.
Proper Aluminum Bearing Bar Support
The bearing bars of the aluminum grating must have adequate support to distribute loads effectively:
For bearing bar depths up to 2-1/4 inches, a minimum bearing of 1 inch is recommended.
For depths of 2-1/2 inches or greater, a minimum bearing of 2 inches is required.
These guidelines help in ensuring that the aluminum bar grating remains securely in place and functions as intended under various loading conditions.
Cutouts for Circular Obstructions
When accommodating circular obstructions, such as pipes or columns, cutouts should be made at least 2 inches larger in diameter than the obstruction. This practice prevents stress concentration around the cutout edges, which could otherwise lead to cracking or weakening of the grating structure. It is also advisable to make field cutouts for all piping with a diameter of 4 inches or less to ensure precise fitting and reduce the risk of damage.
Maintenance and Inspection
Aluminum bar grating is renowned for its low-maintenance requirements, making it ideal for demanding environments. However, regular inspections are essential to ensure long-term performance:
Inspect for signs of wear, corrosion, or damage, particularly in high-traffic or corrosive environments.
Promptly address any minor issues, such as loose connections or bent bars, to prevent further damage.
By performing routine maintenance checks, the longevity and safety of the grating are significantly enhanced.
Corrosion Resistance and Suitability for Harsh Environments
Due to its inherent corrosion resistance, aluminum bar grating is a preferred choice for environments prone to high moisture or chemical exposure, such as water treatment plants, marine settings, and chemical processing facilities. The aluminum material’s natural oxide layer provides robust protection against corrosion, reducing the need for frequent maintenance or replacement.
ADA Compliance and Accessibility Considerations
For installations in public or commercial spaces, compliance with the Americans with Disabilities Act (ADA) is critical:
Grating with a maximum opening of 1/2 inch should be used.
The elongated openings must be installed perpendicular to the direction of travel to prevent tripping hazards and ensure accessibility for all users, including those with mobility aids.
Proper installation of ADA-compliant grating enhances safety and accessibility, making the environment more inclusive.
Safety Enhancement Through Proper Grating Selection
Choosing aluminum bar grating that meets the recommended standards and guidelines can significantly enhance safety and usability for all users. In addition to its strength and corrosion resistance, aluminum bar grating offers versatility for various architectural and industrial applications, combining aesthetic appeal with functional reliability.
Conclusion
Adhering to these installation practices for aluminum bar grating in New York ensures a durable, safe, and compliant installation. Proper planning, correct material selection, and adherence to guidelines are crucial for maximizing the performance and longevity of aluminum bar grating in any setting.
Comments
Tags
Frequently Asked Question
Aluminum bar grating should be installed with the cross rods positioned on the top side. This orientation is crucial for meeting the manufacturer’s strength specifications and ensuring the grating can handle the designed load capacity.
For bearing bar depths up to 2-1/4 inches, a minimum bearing of 1 inch is recommended. For depths of 2-1/2 inches or greater, a minimum bearing of 2 inches is required. These guidelines help distribute loads effectively and maintain structural stability.
When creating cutouts for circular obstructions like pipes or columns, the cutouts should be at least 2 inches larger in diameter than the obstruction. This prevents stress concentration around the edges, reducing the risk of cracking or weakening of the grating structure.
Regular inspections are recommended to check for signs of wear, corrosion, or damage, particularly in high-traffic or corrosive environments. Addressing minor issues, such as loose connections or bent bars, promptly can prevent more significant problems and extend the grating’s lifespan.